In the News
Posted on April 16, 2020
On one end of the state, crews built temporary patient rooms in a hospital.
On the other end, they’re working on a major bridge project and getting ready to tackle a season’s worth of construction.
“Like any business, the COVID-19 pandemic immediately and significantly changed the way we view our role, but it’s also providing us an opportunity to truly be of service to our clients and our communities while making sure we’re keeping our employees safe,” Journey Group CEO Randy Knecht said.
“I’ve been proud to see how our teams have responded, how they keep their work moving forward and how they’re ready to change gears at a moment’s notice if it means we can help.”
Quick response
As Monument Health in Rapid City began to anticipate a need for more patient rooms in March, its construction management team reached out to Ainsworth-Benning Construction, a division of Journey Group located in Spearfish that serves the Black Hills and surrounding areas.
“Our team immediately got to work building out temporary rooms in existing shell space,” said Bob Morcom, Ainsworth-Benning division leader. “Our Ainsworth-Benning team put in a 12-hour day after getting the initial call, laying out a plan, framing, installing blockings, sheetrocking and taping walls.”
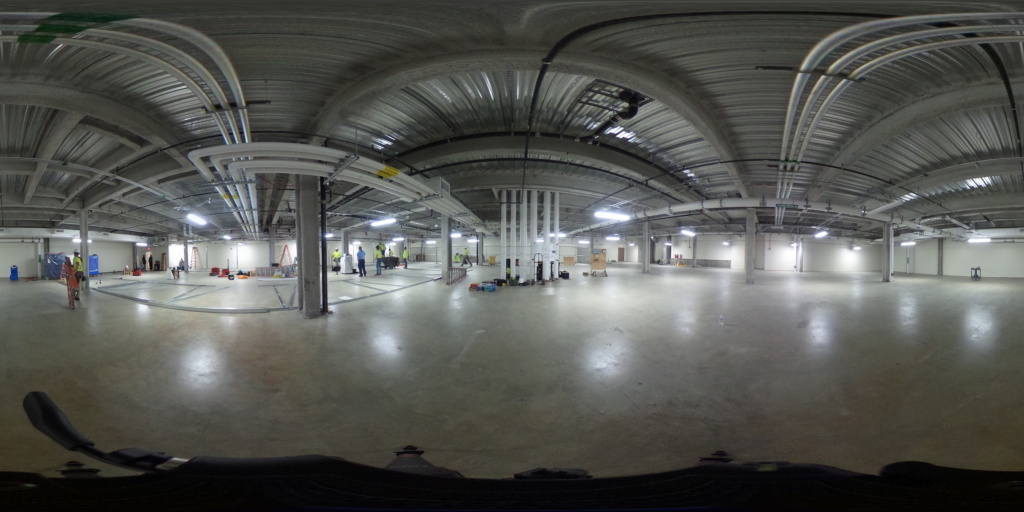
The next day – a Saturday – Ainsworth-Benning returned to finish taping, brace walls and paint. By Monday, the team was helping Monument Health move equipment into the future patient rooms.
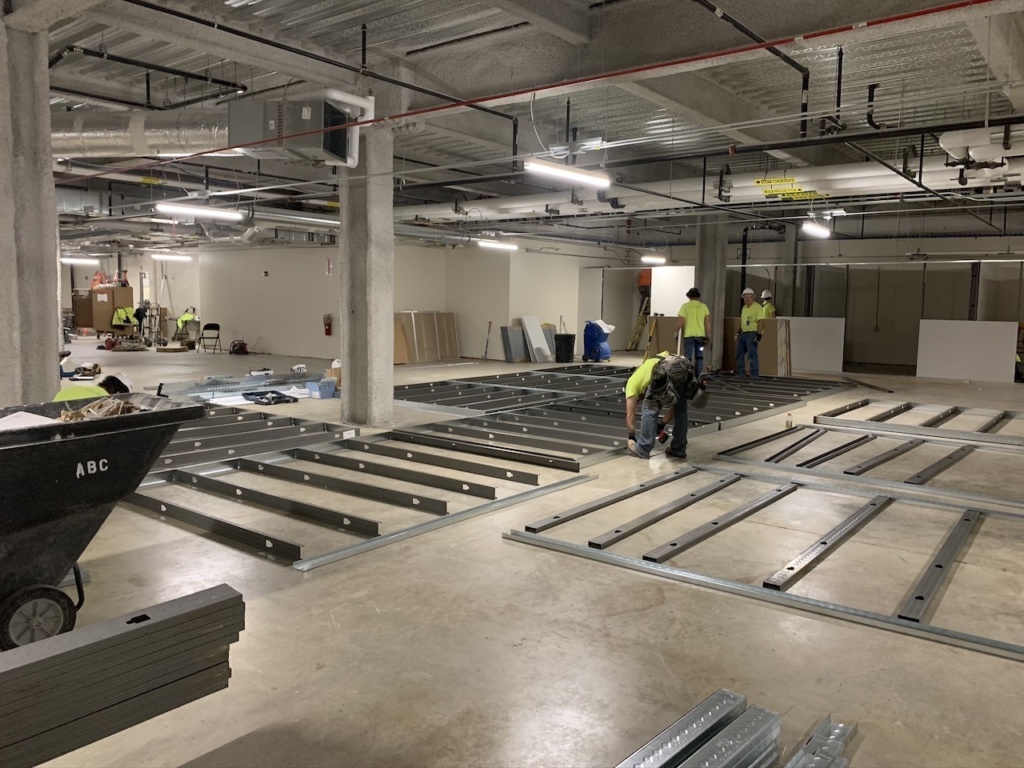
“Overall, our scope of work was completed in 16 hours,” Morcom said. “I’m incredibly proud of our team’s fast turnaround while maintaining our standards of safety and quality.”
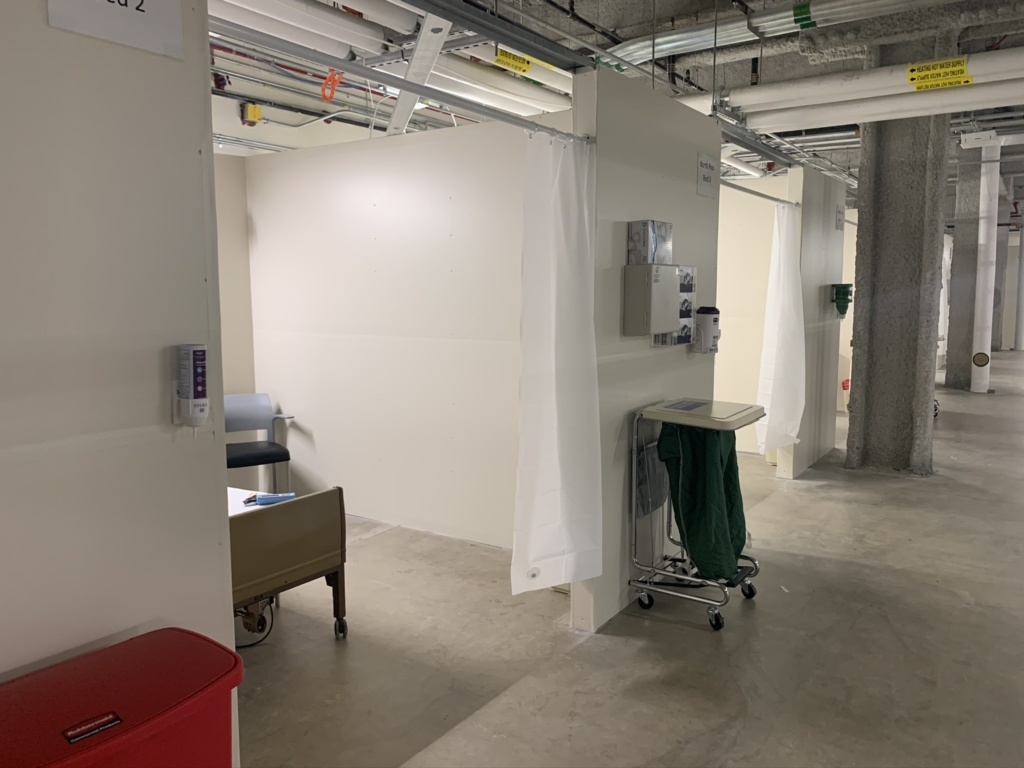
The following week, Ainsworth-Benning was called on again to construct an additional 20 temporary patient rooms in a different shell space. Layout and material procurement started immediately, and Don Werner, project manager, quickly contacted Midwestern Mechanical for plumbing and medical gas installation.
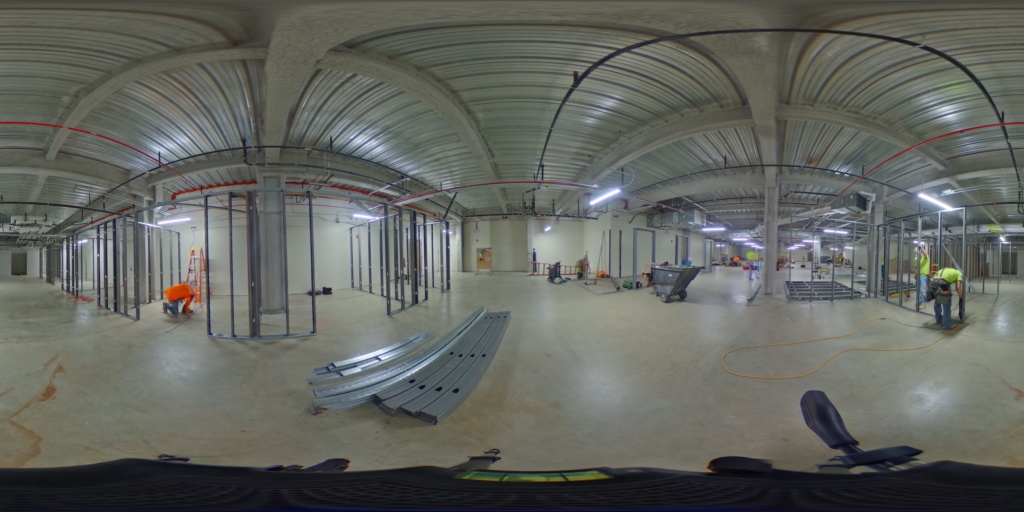
“The next day, a nine-person Ainsworth-Benning crew laid out walls, framed, installed blocking and sheetrocked 90 percent of the walls in 10 hours,” Morcom said. “Midwestern Mechanical got started on two bathrooms, a shower and hand wash sinks and started getting materials for medical gas installation. Within a matter of days, the entire project was done. We’re grateful we were able to assist Monument Health at such a critical time and that they’re now able to focus on other preparations for patients, knowing that these rooms are ready.”
Business as usual
On any given day, there will be a Journey crew at work somewhere on the campuses of Avera McKennan Hospital & University Health Center in Sioux Falls.
That hasn’t changed as the health system is preparing for an influx of COVID-19 patients, said Mark Lukonen, senior project manager.
“It’s more or less business as usual. We’re staying focused, our people are continuing to work, and our existing projects for Avera are moving forward,” he said. “Avera has good capacity in its facilities and can shift patients around. We’ve expanded some of the capacity in the ICU rooms to make more isolation rooms, which will directly aid in efforts if there is an influx of patients.”
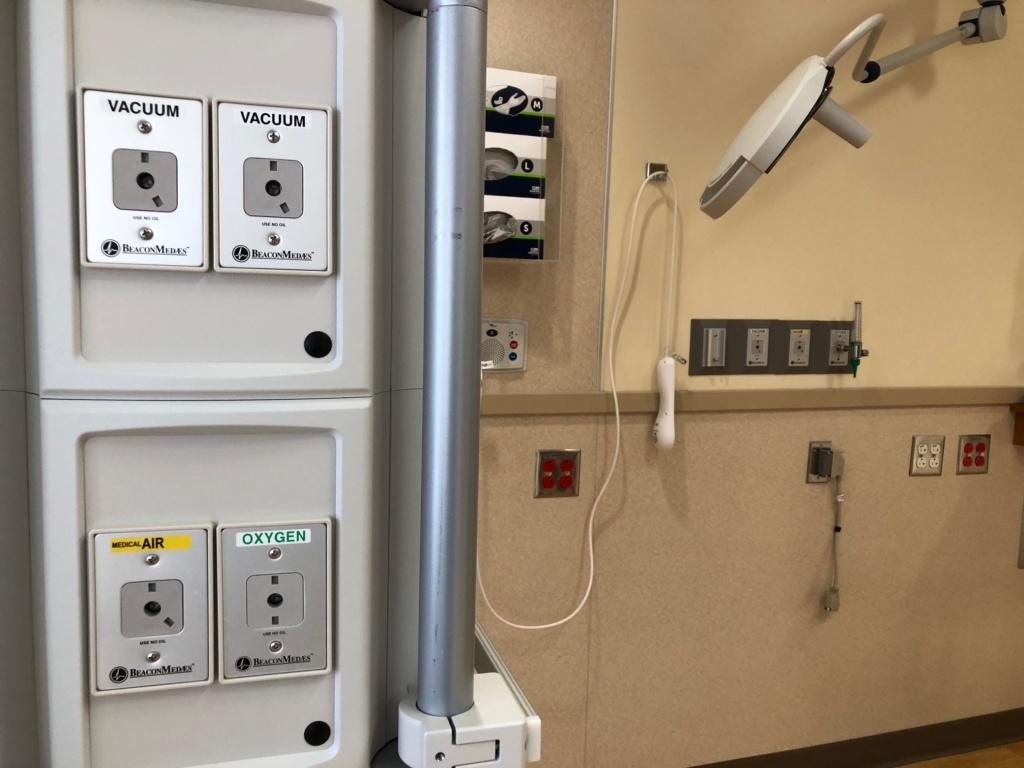
Journey has worked on multiple wings in the ICU to expand capacity with negative pressure systems, which help keep contaminated air contained.
“Our team in the hospital feels good about being there,” Lukonen said. “Avera has hand sanitizer all over. They have employees actively wiping down high-touch areas like door handles and elevator buttons. We feel safe there, and Avera has been a great help in that regard.”
Journey also was able to donate 300 N95 respirators to Avera from its inventory.
The Journey team is continuing with renovations to some surgical areas, an inpatient rehab project and other small projects.
“We do 100 to 120 projects a year at Avera, from swapping out doors to major renovations like the surgical suites,” Lukonen said. “We’re moving forward, and we know where we’re able to work safely and where we shouldn’t be.”
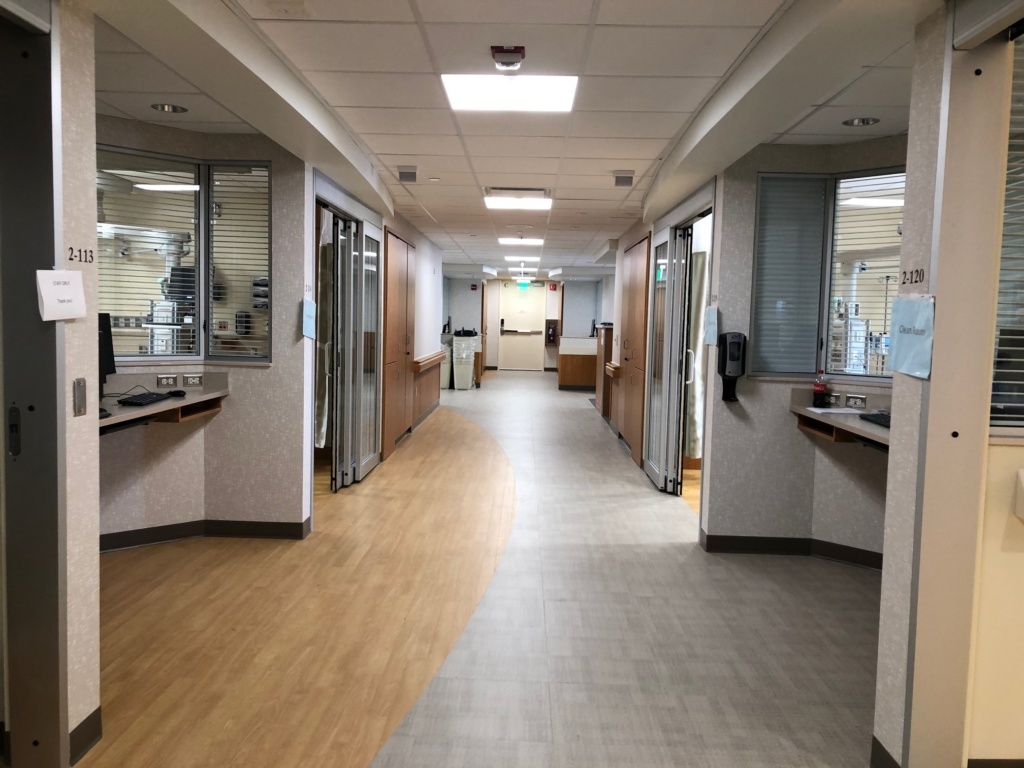
Staying safe
Other major construction projects throughout Journey Group are moving ahead with extra precautions being taken in the field.
SFC Civil Constructors, a Journey division, started work in March on the rehabilitation of the downtown Eighth Street bridge.
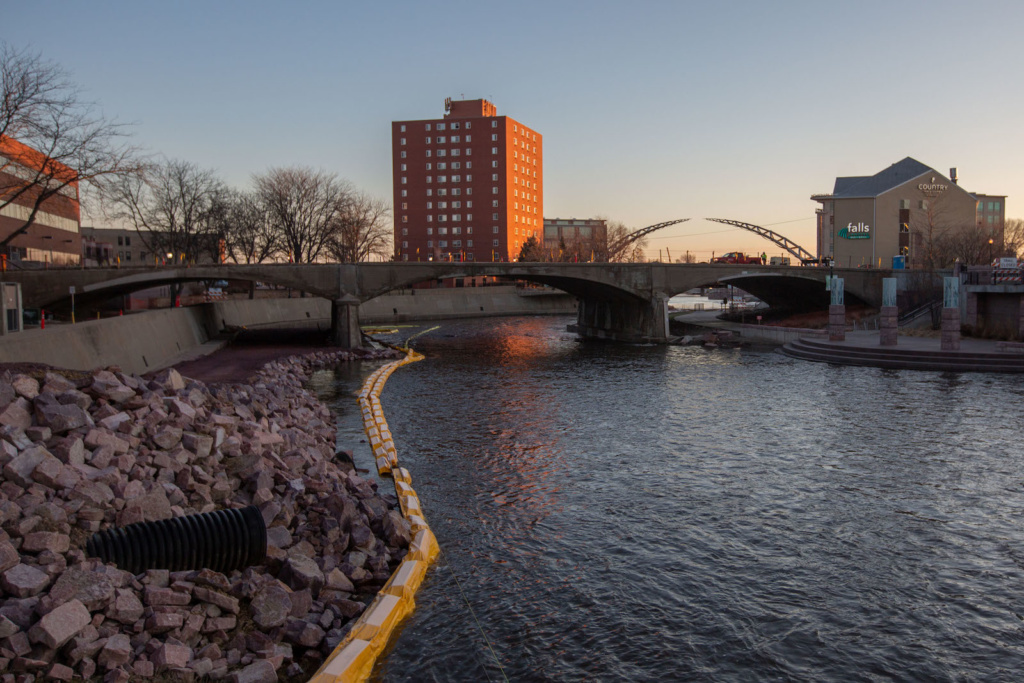
Daily huddles at the job site look a bit different now, with team members spaced far apart and the conversation always circling back to safety.
“We’re trying our best to keep them updated and educated. We’re trying everything we can to keep working and keep everyone healthy,” said Joel Van Ekeren, Journey’s safety director.
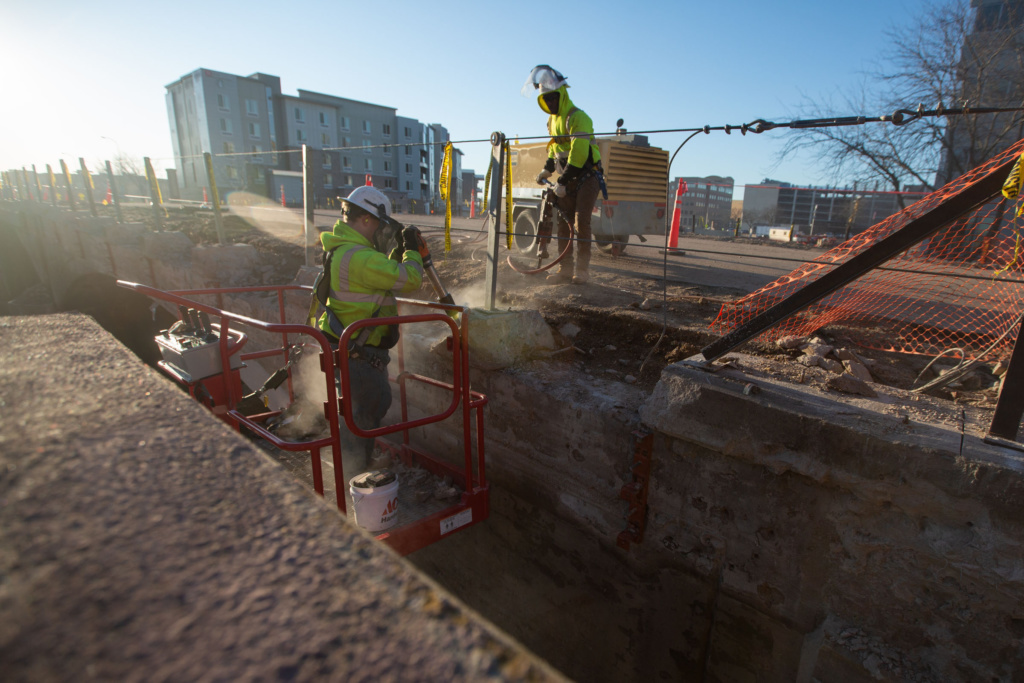
“They’re outside, and they’re staying a good distance from each other. We’re asking them to take breaks in their car. We are thankful it’s not winter and 30 below zero.”
Journey has significantly increased communications and oversight of personal hygiene requirements for employees and has limited visitors to drive better prevention practices. The company also has implemented additional routine environmental cleaning to all workplace surfaces, equipment and tools.
In addition, there are newly installed wash stations with the restrooms on every job site along with hand sanitizer dispensers.
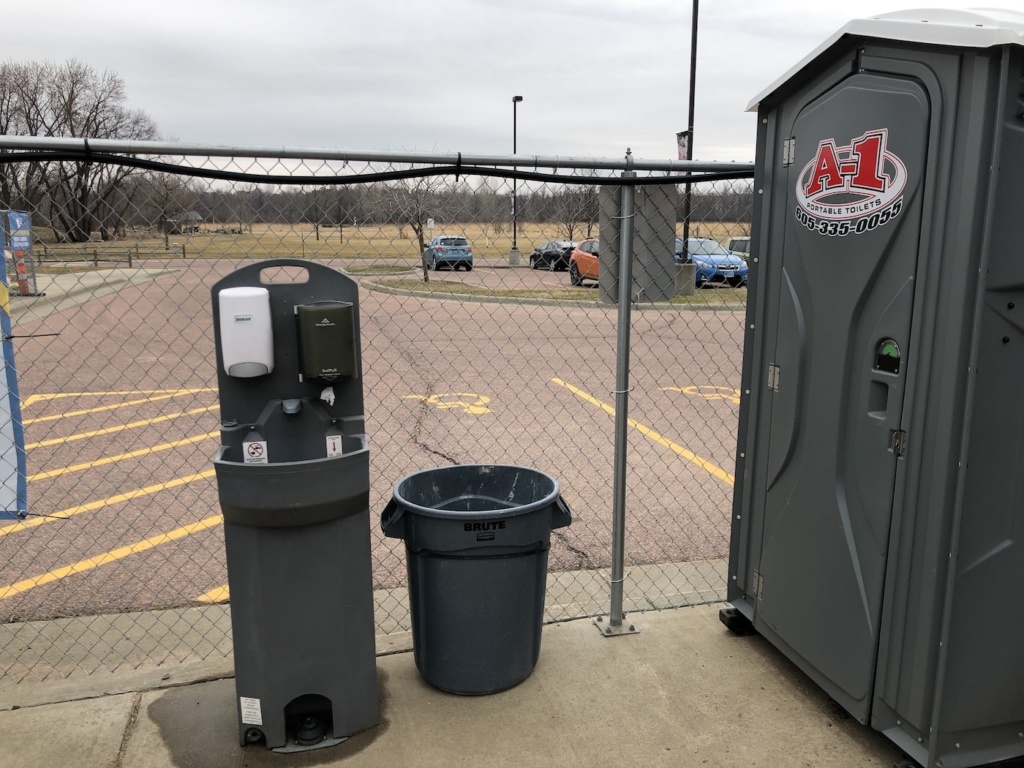
“That was huge, and we’re going to keep doing that even after this passes,” Van Ekeren said.
After a safety orientation, Journey’s team and its subcontractors get a sticker to show they have received the information, which includes a reminder on how to stop the spread of COVID-19.
“They’re all responding well,” Van Ekeren said. “Everyone has a lot on their mind. Most of them have kids now home from school, and they’re figuring out how to balance that with their spouse. The big thing is just talking about how we’re still working and they’re still getting a paycheck, which is a really good thing. We want to keep them focused because that’s important for safety. I’m trying to keep it as normal as possible.”